As the apparel market matures, consumer demands for garment quality intensify. To meet these expectations, apparel enterprises must embrace a “Quality-Centric” approach, meticulously managing every step of the production process. This comprehensive quality control extends from raw materials to final products, ensuring the stability of production factors and delivering high-quality garments to customers. This article provides recommendations for quality management in apparel production, focusing on various aspects.
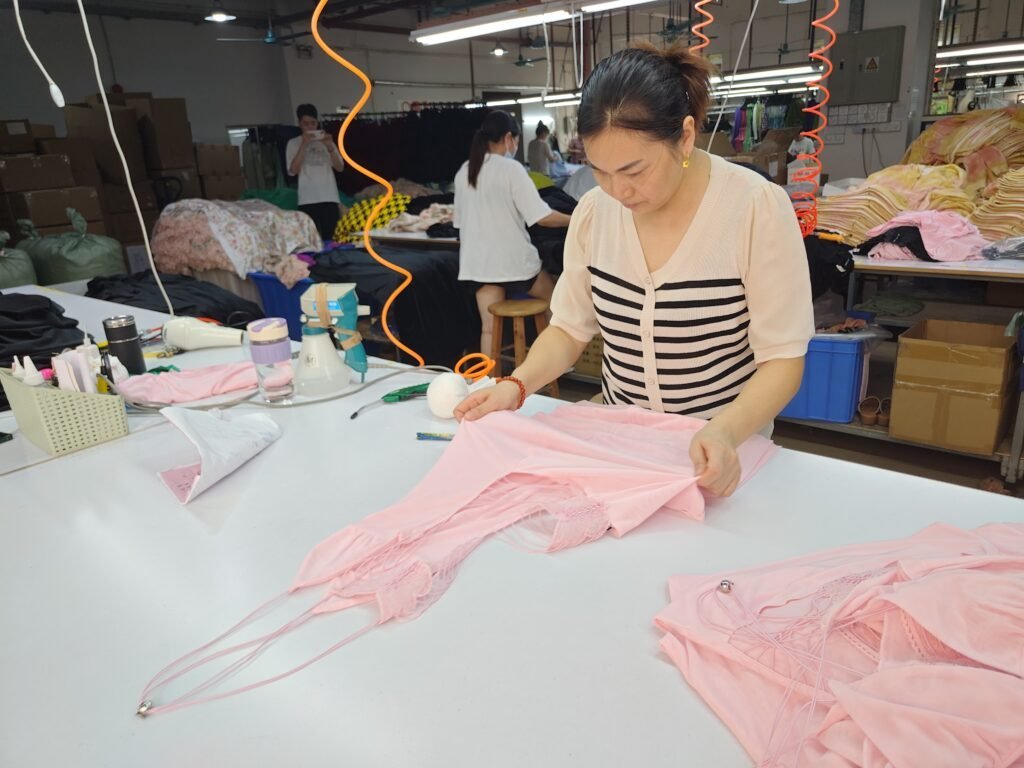
I. Quality Control Processes and Content in Apparel Production
1. Quality Control of Raw Materials
In the realm of apparel production, meticulous quality control of raw materials is a cornerstone in ensuring the integrity and excellence of the final products. Raw materials encompass fabrics, linings, and an array of accessories, from interlinings and fillings to sewing threads, buttons, zippers, and labels. This comprehensive scrutiny adheres to established product standards and technical contracts.
Upon receiving shipments, a representative sample undergoes rigorous examination, encompassing factors like composition, manufacturing structure, width, weight, and performance metrics such as shrinkage, colorfastness, and strength. Assessments extend to detecting color variations, fabric defects, and overall pass rates, ensuring alignment with specified standards.
Recognizing the pivotal role of raw material quality control, contemporary practices place heightened emphasis on safety, health, and environmental considerations. Monitoring formaldehyde content, avoiding prohibited aromatic adhesives in dyes, and addressing potential environmental impacts highlight the commitment to responsible manufacturing.
2. Quality Control of Cutting and Sewing Equipment
In the intricate dance of apparel production, the quality control of cutting and sewing equipment emerges as a linchpin for precision and excellence. Cutting machinery, including vertical electric scissors, belt cutting machines, and drilling machines, or even the modern marvel of automatic cutting beds, plays a crucial role. Complementary tools like hand scissors, pressing devices, and measuring instruments are equally indispensable. For these mechanical wonders, quality control revolves around regular and irregular maintenance, ensuring both external cleanliness and the seamless operation of internal components and cutting tools. A delicate balance of precision and intact performance must be maintained.
Sewing equipment, ranging from straight sewing machines and overlock machines to decorative sewing machines like double and four-needle machines, adds another layer to the production symphony. With technological leaps, specialized equipment such as bartackers, automatic bag-opening machines, and sleeve-setting machines have become commonplace in the assembly line. Before the mass production gears up, meticulous maintenance and fine-tuning of sewing equipment are prerequisites for ensuring flawless operation.
Quality control for sewing equipment extends beyond initial setup. It involves continuous adjustments based on fabric and lining textures, needle pitch density, and pressure on sewing machine feet. This meticulous approach prevents stitching irregularities and ensures that the final product meets the standards of texture, durability, and aesthetic appeal.
In essence, the quality control of cutting and sewing equipment is not just a checkpoint; it’s a dynamic process that threads precision into every stitch and cut, ensuring the garments meet the highest standards of craftsmanship.
3. Quality Control in Production Processes
In the realm of apparel production, meticulous quality control throughout the production processes is the linchpin for crafting garments of unparalleled excellence. The production of clothing involves a sophisticated division of labor, where various standardized garments are disassembled into multiple meticulous processes and workstations, creating a seamless flow of operations. Strengthening the quality control at each production stage ensures not only the localized excellence of each garment component but also the overall quality of the final product.
The overarching apparel production process can be categorized into cutting, sewing, fastening, handcrafting, and finishing and packaging. Each of these segments comprises numerous small-scale quality control points. For instance, in the cutting phase, fabric inspection, pattern inspection, and numbering serve as critical quality checkpoints. Similarly, sewing involves foundational workflows, component fabrication workflows, and assembly workflows, each with its set of quality control points.
Quality control in apparel production is not only the responsibility of dedicated quality inspectors but involves the active participation of all production operators. Following the principle of “downstream workflows supervising upstream workflows, downstream processes supervising upstream processes,” every operator plays a crucial role in implementing and reinforcing quality control requirements. This collaborative effort ensures that any deviations from the prescribed quality standards are identified and rectified promptly, preventing the propagation of quality issues throughout the production process.
4.Quality Control in Finished Product and Factory Departure Inspections
Quality control through final inspections, encompassing both the finished product inspection and factory departure inspection, stands as critical checkpoints in the apparel production process. The finished product inspection involves a meticulous examination of each garment, typically conducted before packaging and boxing. This process aims to identify items that deviate from product standards and operational requirements. By isolating non-conforming items, subsequent rework or downgrading procedures can be implemented, thereby enhancing the overall compliance or excellence rate of the entire batch of apparel products. Categorizing and handling non-conforming items allows for efficient resource utilization and waste reduction while ensuring quality.
On the other hand, the factory departure inspection utilizes a sampling approach, where factory-level inspectors or customer-designated inspectors assess the quality of packaged and boxed apparel products ready for shipment. The inspection results determine whether the entire batch of finished products meets the required quality standards and is fit for shipment. This final inspection serves as the last line of defense in quality control during the production process, not only ensuring product quality and maintaining the company’s reputation but also evaluating the effectiveness of quality control at earlier production stages. Generally, the absence of significant quality issues in the departure inspection signifies the effectiveness of quality control measures implemented throughout the preceding production processes.
II. Several Issues to be Considered in the Implementation of Quality Control in the Production Process of Clothing Enterprises
1. Recognizing the Significance of Quality Control
In the intricate process of implementing quality control within a clothing enterprise’s production process, the initial step involves business operators fully recognizing the paramount significance of quality control. This recognition spans from the intake of raw materials to the dispatch of finished products, encompassing various departments such as planning, supply and sales, technology, and production quality inspection.
2. Upholding Product Quality as Enterprise Lifeblood
A crucial aspect for business operators is to perceive product quality as the lifeblood of the enterprise. This recognition is foundational, establishing a belief in comprehensive quality management throughout the entirety of the production process. Providing robust assurance for quality control measures in terms of systems, organization, and actions becomes imperative to ensure a seamless and effective implementation.
3. Empowering Quality Inspection Department
Conflicts between production schedules and product quality demand prioritization of the latter. Business operators should uphold the absolute authority of the quality inspection department, empowering it with the “veto power” to prevent the spread of quality issues, eliminate influencing factors, and prevent non-compliant products from leaving the factory. This empowerment ensures that quality control serves as a genuine gatekeeping role in the production process.
4. Fostering Quality Responsibility Among Personnel
Fostering a sense of quality responsibility among relevant personnel emerges as a vital consideration. Through means such as publicity and training, integrating quality control measures into daily work becomes imperative for all personnel associated with clothing production. From business and production management to technical quality management and line operators, every individual should consciously integrate specific quality control requirements into their responsibilities.
5. Establishing Comprehensive Responsibility Systems
The establishment of comprehensive responsibility systems is crucial for effective quality control. By formulating position responsibility systems, clear definitions of job positions and their responsibilities in terms of quality control are outlined. These responsibilities are further subdivided into leadership, technical quality management, and production operation responsibilities. This meticulous categorization ensures specificity during system implementation, facilitating traceability and compliance.
6. Linking Responsibility Systems to Economic Assessment
Linking responsibility systems to relevant economic assessment indicators adds a layer of accountability. Regular inspections assessing the effectiveness of quality control provide conditions for rewards and penalties based on the quality control status. This linkage ensures that economic considerations align with the commitment to maintaining high-quality standards throughout the production process.
7. Authoritative Department Inspection
The authoritative department responsible for quality management, such as the Comprehensive Quality Management Office or Quality Assurance Office, plays a pivotal role. Regular inspections serve a dual purpose: understanding the effectiveness of current quality control and identifying areas for further management and adjustment. This department promptly provides relevant information to business operators, summarizing experiences and formulating measures to enhance the meticulousness and perfection of quality control in the production process.
In conclusion, quality control in the production process is not just a checkpoint; it is an indispensable and important management tool for clothing production enterprises. Its implementation and reinforcement ensure not only product quality but also the continuous improvement of the enterprise’s management level and production capabilities. This approach contributes to the enhancement of work efficiency and the steady strengthening of the company’s competitiveness.